Induction hardening machines for all requirements
VECTOR | VERTIKALE HÄRTEMASCHINE
Why this system concept for steering racks?
ThermProTEC has developed the Vector hardening machine type especially for the manufacture of steering racks. With this hardening system the process steps hardening and tempering are carried out in this plant. Precise process control is essential for the surface hardening of steering racks. The penetration depth and the deformation of the teeth are of particular importance here.
System design
All axes of our systems are CNC controlled and specially shaped inductors with field concentrators are used. The distance between the inductor and the component is continuously measured and readjusted during the feed process. At the same time, a special ring shower arrangement is integrated in this feed process, which ensures the required high quenching and tempering quality. Both measurement and positioning are carried out in two axes, CNC controlled. In order to be able to implement a safe process sequence without the risk of mix-ups, the entire structure was realized with a rotary table. Both thermal processes, hardening and tempering, are connected to the guide systems via a central vertical axis.
Heating technology
An induction generator with two individual oscillating circuits is used. A special feature of this system are three permanently installed servo axes for the rotation, which are located on the rotary table and rotate continuously. Both the power supply and the control of these drives are effected via a slip ring connection, which is also guaranteed by the Profinet. The vertical axes of the two heating circuits are also integrated into the CNC network of the Siemens Sinumeric control system. The coupling of the processes with the rotary indexing table ensures that all components pass through the tempering process. In this system, the tailstock tips can also be adjusted via a servo axis, with the actual clamping being performed via pneumatic tips. The quenching medium is collected in a tank below the rotary indexing table and fed to the central tank via a fleece filter system. All process parameters are continuously monitored. The quenching water quantities are recorded, including Brix concentration, temperature and energy quantity during the process.
Hardening & tempering combined
The system is divided into three parts with the rotary table, loading is carried out from the front, manually or robot-controlled. The components are clamped with a pneumatic prism system and the correct positioning is checked via a measuring system in the clamping head.
The system includes an electrostatic filter system as well as an optional blow-off system for residual water before withdrawal. The basic version of the induction generator has an output of 180 kW (150 kW hardening, 30 kW starting) in the frequency range of 6-10 kHz. The system has proven itself many times in this application and is used by leading manufacturers of steering systems worldwide. Based on this concept, systems for other components, such as large shafts, have also been realised.
You are interested, have questions or suggestions?
Our team is at your disposal. We look forward to your message!
Zunftstr. 20 | 77694 Kehl-Marlen | DE
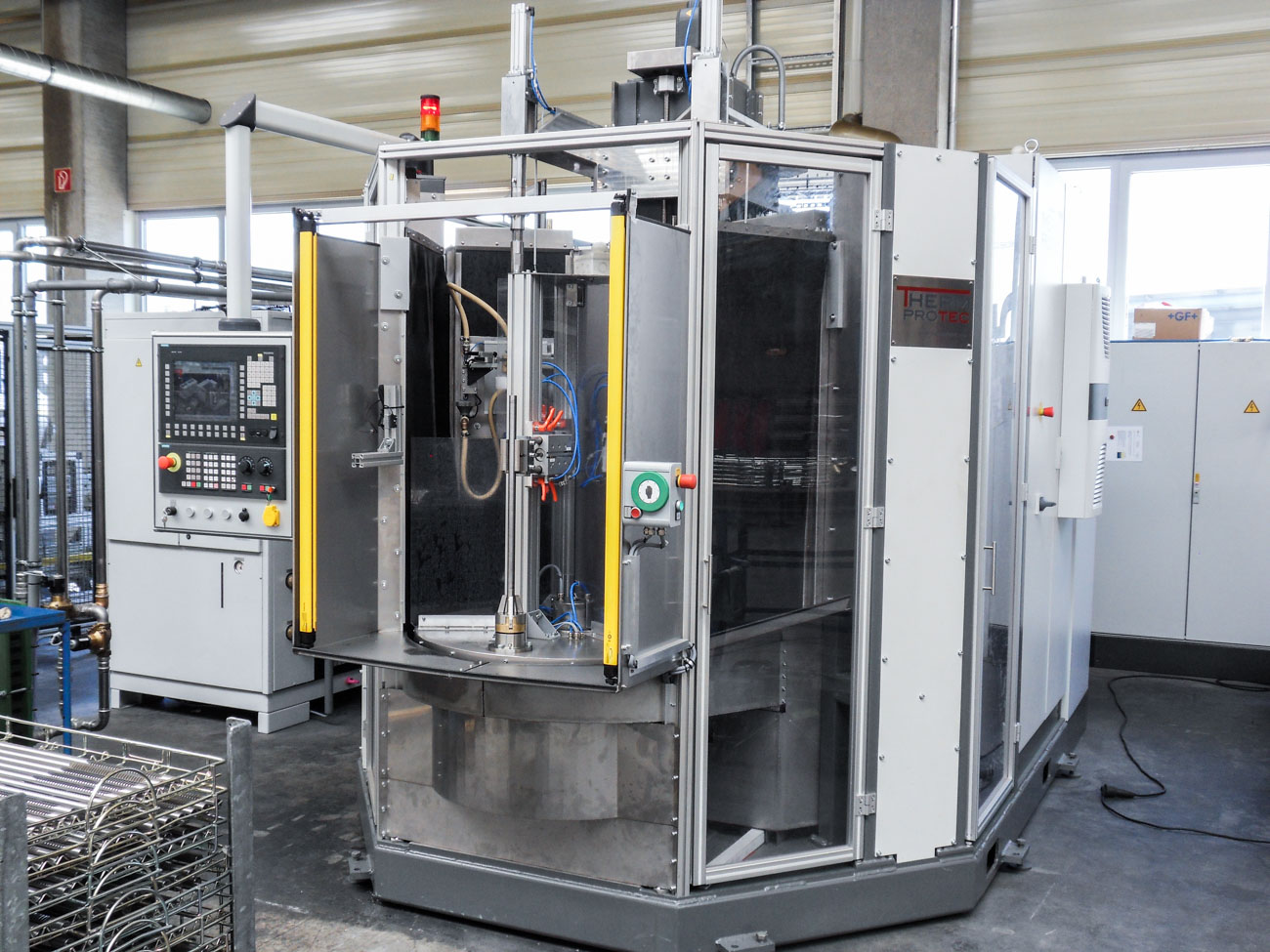
Related products:
Useful links
Contact